Hajdu highlights Lytton First Nation housing and disaster recovery investments
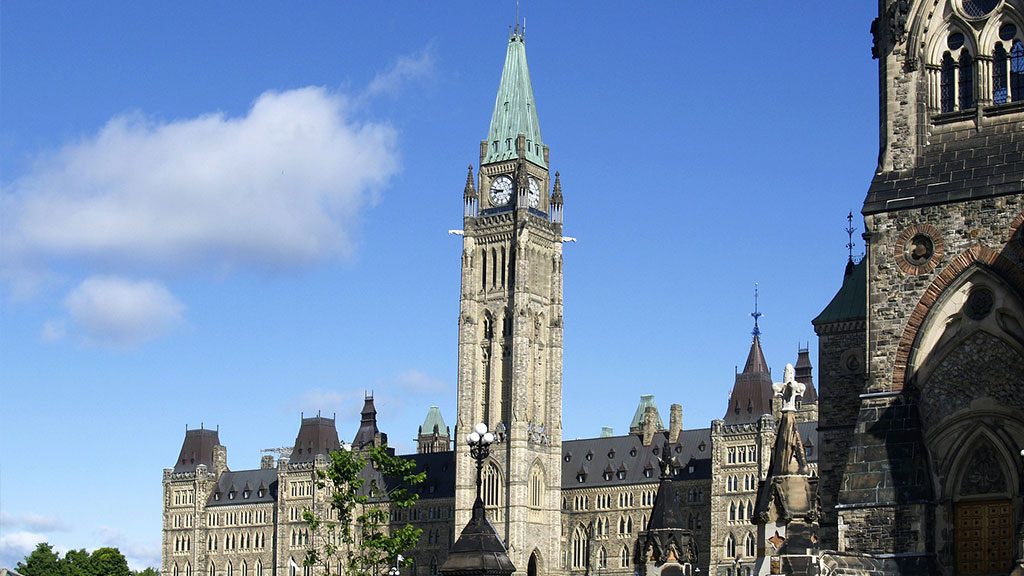
Hajdu highlights Lytton First Nation housing and disaster recovery investments
LYTTON FIRST NATION, B.C. – Federal Minister of Indigenous Services Canada Patty Hajdu recently announced investments in Lytton First Nation in British Columbia. Hajdu visited Lytton First Nation on April 24 to announce $1.3 million through the Housing A...
Government , Infrastructure
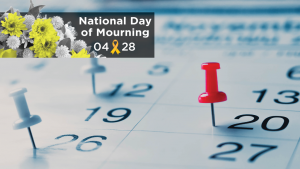
Canadian Labour Congress Day of Mourning events – Western Canada
OTTAWA — Every year on April 28, thousands of workers, friends and families of w...
Labour , OH&S
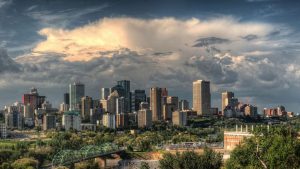
City of Edmonton releases final draft of District Policy
EDMONTON – The City of Edmonton has released the final draft of its District Pol...
Government
The Construction Record Podcast – Special: Federal Budget Reactions
On this episode of The Construction Record Podcast, digital media editor Warren...
Certificates
Published Certificates and Notices
Tenders
Tenders for Construction Services
Latest News
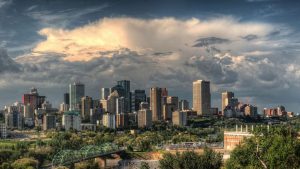
City of Edmonton releases final draft of District Policy
EDMONTON – The City of Edmonton has released the final draft of its District Pol...
Government

Hajdu highlights Lytton First Nation housing and disaster recovery investments
LYTTON FIRST NATION, B.C. – Federal Minister of Indigenous Services Canada Patty...
Government , Infrastructure
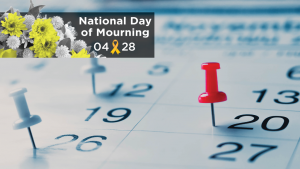
Canadian Labour Congress Day of Mourning events – Western Canada
OTTAWA — Every year on April 28, thousands of workers, friends and families of w...
Labour , OH&S
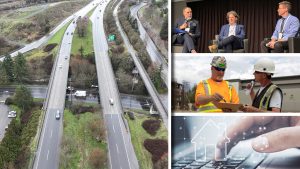
Your top JOC headlines: April 22 to 26
Your top JOC headlines this week feature our North American housing crisis cover...
Associations , Economic , Infrastructure , OH&S , Resource
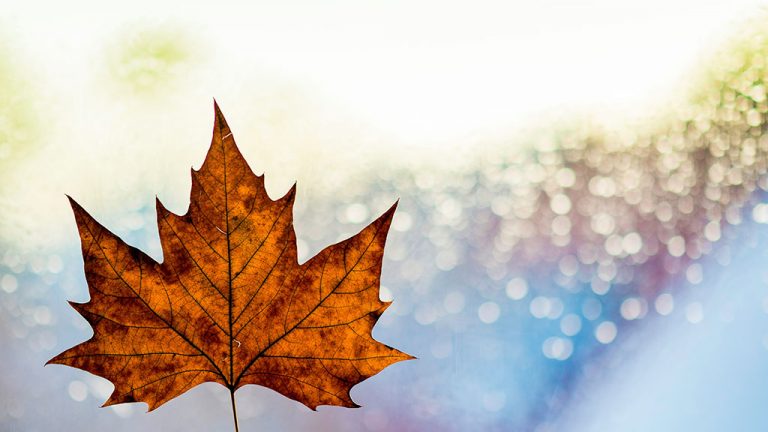
Pedro Barata named new president and CEO of Habitat for Humanity
TORONTO — Pedro Barata will be taking over the role of president and CEO of Habi...
Economic
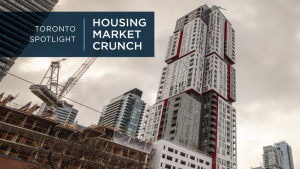
The devil’s in the details of federal funding for Toronto housing
How many dollars of federal funding will directly create new housing units depen...
Economic , Government
The Construction Record Podcast – Special: Federal Budget Reactions
On this episode of The Construction Record Podcast, digital media editor Warren...
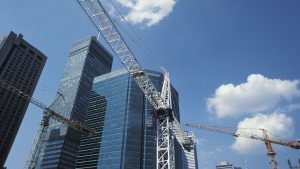
Top 10 largest construction project starts in Canada – March 2024
The accompanying table records the 10 largest construction project start...
Economic , Projects
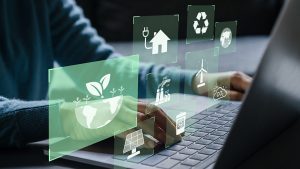
BuildForce Canada report looks at impact of retrofitting buildings to achieve net-zero goals
OTTAWA — A new report prepared by BuildForce Canada considers the impact of retr...
Economic , Resource
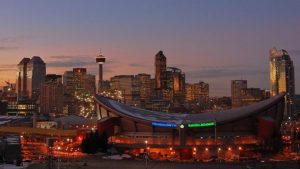
Calgary Construction Association reaffirms support for city’s housing strategy
CALGARY – The Calgary Construction Association (CCA) has announced it continues...
Associations , Government
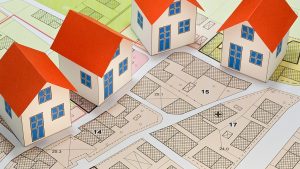
B.C. selects next communities for housing targets
VICTORIA – The Government of British Columbia has identified a new set of priori...
Government , Projects
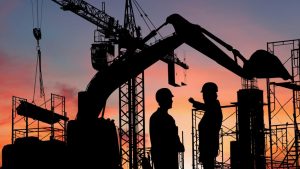
B.C. to increase local milk production with $25-million factory investment
ABBOTSFORD, B.C. — The British Columbia government is spending up to $25 million...
Government , Projects
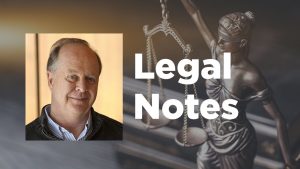
Legal Notes: The liability potential for legal counsel with frivolous liens
The liability consequences can spread beyond the party launching a lien, if it i...
Government
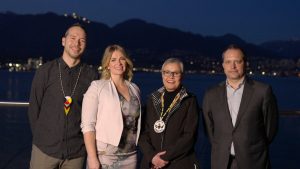
Indigenous project financing plan praised as game-changer
First Nations major project proponents are hailing the establishment of a $5-bil...
Projects
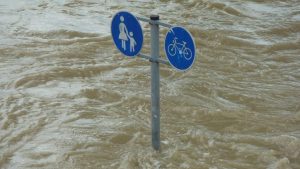
B.C. to improve flood preparation in Township of Langley
LANGLEY, B.C. – The Government of British Columbia is working to improve pump ca...
Infrastructure
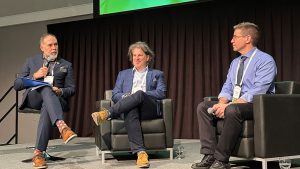
B.C.’s future energy needs require electricity and gas: VICA panellists
British Columbia will need more energy in the future and getting there will requ...
Associations , Resource
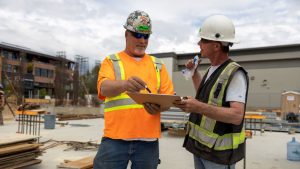
WorkSafeBC announces 2024 approach to inspections
RICHMOND, B.C. – WorkSafeBC is indicating an emphasis on inspections in 2024 as...
OH&S
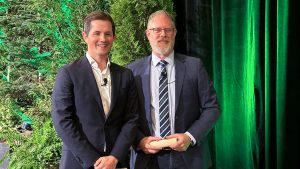
Increased wildfire threats raise public awareness of forestry industry: expert
A public opinion expert sees both opportunity and new challenges as British Colu...
Resource
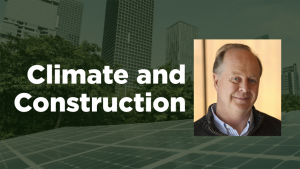
Olympic Stadium gains respectability through roof recycling competition
Montréal’s 1976 Olympic Stadium roof has had a troubled life from its conception...
Projects , Resource
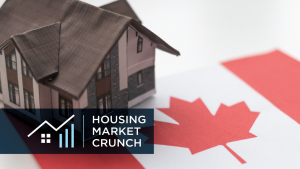
Federal housing money too little too late for some stakeholders
The federal government’s $4 billion national Housing Accelerator Fund (HAF) is “...
Associations , Government
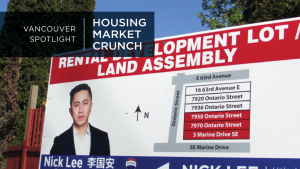
Land and development issues mire affordable Vancouver housing
Vancouver’s affordable housing deficit is mired in development issues, land shor...
Economic , Government
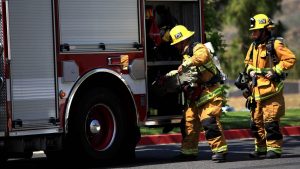
Fire destroys Second World War hangar at former Edmonton airport
An aircraft hangar built during the Second World War at Edmonton's former munici...
Infrastructure , OH&S
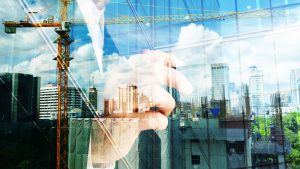
Top 10 major upcoming High-Rise Residential and Transportation construction projects – Canada – April 2024
The accompanying tables show the top 10 largest upcoming High-Rise Residential a...
Economic , Projects
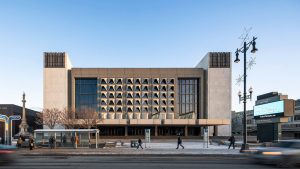
Heritage Winnipeg Preservation Award winners announced
WINNIPEG – The winners of Heritage Winnipeg’s 38th annual Preservation Awards ha...
Projects
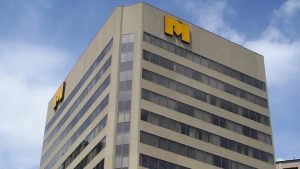
Phipps-McKinnon building in Edmonton to become partial residential conversion
EDMONTON – Edmonton’s Phipps-McKinnon building is set to become a partial office...
Projects
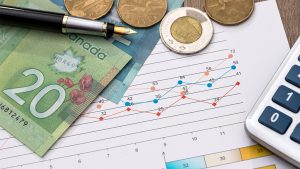
B.C. funds rural Kootenay economic development
RADIUM HOT SPRINGS, B.C. – The Government of British Columbia is funding local g...
Government
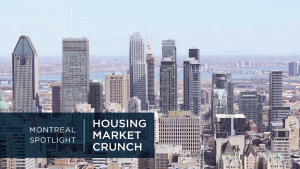
Rental market spurring Montreal housing construction
The Montreal housing market has seen a sharp increase in rental construction ver...
Economic
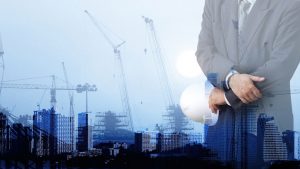
Top 10 major upcoming Residential and Transportation Terminal construction projects – U.S. – April 2024
The accompanying tables show the top 10 largest upcoming Residential and Transpo...
Projects
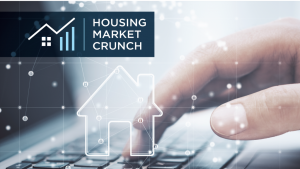
News Tracker: North America’s Housing Crisis
It’s no secret North America is in the throes of a housing crisis with governmen...
Economic , Government , Labour , Projects , US News
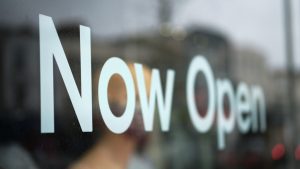
New women’s transition and child care housing complex opens in Kitimat
KITIMAT, B.C. – A new development opening in Kitimat, B.C. will provide 44 homes...
Projects
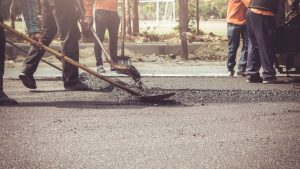
Manitoba invests $3.8 million in Dauphin main street reconstruction
DAUPHIN, MAN. – The Government of Manitoba is putting $3.8 million towards recon...
Infrastructure
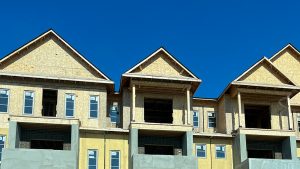
Saskatchewan urban housing starts rise 12.1 per cent
REGINA – Saskatchewan’s urban housing starts rose 12.1 per cent in March 2024 co...
Economic
Most Read News
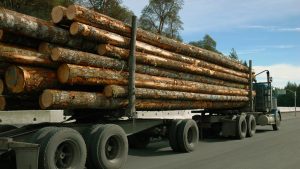
B.C. ups investment in forestry sector with $70.3M in funding
VANCOUVER – The Province of British Columbia has announced a capital investment...
Government , Resource
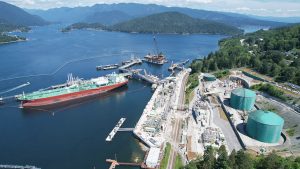
Done: Expanded Trans Mountain pipeline launches May 1
Four-and-a-half years after construction began, one of Canada’s most controversi...
Infrastructure , Projects , Resource
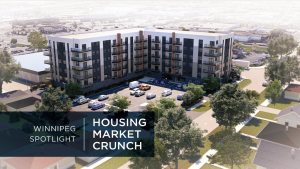
Winnipeg promotes infill development to reduce affordable housing shortage
In his recent State of the City address, Winnipeg Mayor Scott Gillingham says lo...
Economic
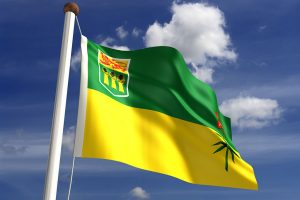
Saskatchewan water agency invests in key infrastructure projects
REGINA – Saskatchewan’s Water Security Agency (WSA) is working on more than 60 w...
Government , Infrastructure
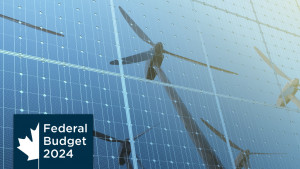
Federal budget introduces, elaborates on clean technology tax credit plans
The 2024 federal budget is re-emphasizing the government’s commitment to a globa...
Government , Resource
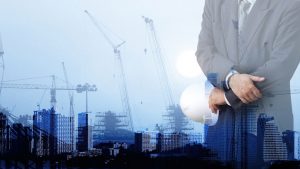
Top 10 major upcoming Residential and Transportation Terminal construction projects – U.S. – April 2024
The accompanying tables show the top 10 largest upcoming Residential and Transpo...
Projects
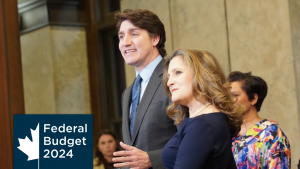
New housing spending dominates Budget 2024
Federal Finance Minister Chrystia Freeland reiterated her government’s recent he...
Economic , Government , Projects
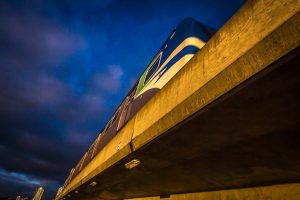
Preferred proponent announced for Surrey Langley Skytrain station construction
SURREY, B.C. – South Fraser Station Partners has been chosen by the Government o...
Government , Infrastructure , Projects
From ConstructConnect
Latest Infographics
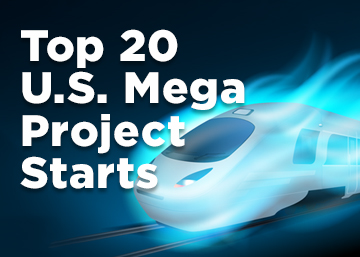
Top 20 U.S. Mega Project Starts
In 2020, there were 11 projects valued at $1 billion or more each, and 26 projec...
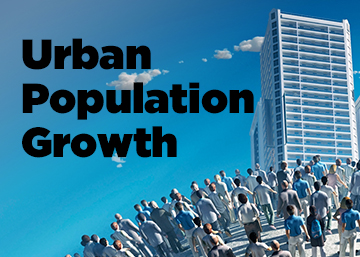
Canada's Urban Population Growth
This infographic looks at the surge in Canada's urban population growth.
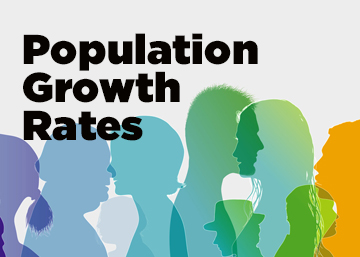
Canadian Demographics
This infographic looks at the latest Canadian population growth rates.